Sugar Production
Sugar comes from two main crops: sugar cane and sugar beet. As one of the oldest in the world, the indigenous people of New Guinea started it in 8000 BC. Because of its benefits, sugar is often added to the key and key in the sugar strainer. In 1751, America’s first sugar cane was planted in Louisiana, marking the beginning of the American sugar industry, which now provides 142,000 jobs in 22 counties.
Sugar is produced in more than 120 countries; Sugarcane makes up about 80% of sugar production, with sugar beets accounting for the rest. In the United States, 55% of sugar production comes from sugar beets and 45% from sugar cane. According to the United States, global sugar production is expected to exceed 188 million tons this year, up 22 million tons from last year, according to the United States Department of Agriculture. said.
Currently Brazil produces the most sugar (39.5 million tonnes), India (33.7 million tonnes) and the European Union (17.7 million tonnes). The United States is expected to produce 8.2 million tons of sugar this year.
Plantation of Sugar
Sugarcane requires an average temperature of 75 degrees Fahrenheit (23.9 degrees Celsius). In the United States, sugar cane and beet harvesting is done by machine, although in some states it is done by hand. Harvested sugarcane and beets are transported by machine. and truck or rail transport to mills to be processed into raw sugar. Immediately, they are cleaned, washed, ground to remove the juice, filtered and purified.
The result is a clear, sweet drink. In the United States, sugar cane and beet harvesting is done by machine, although in some states it is done by hand. The sugarcane and beets harvested in bulk are loaded onto trucks or railcars and transported to the mills for processing into granulated sugar. Immediately, they are cleaned, washed, ground to remove the juice, filtered and purified. The result is a clear, sweet drink. Celsius) and a rainfall of about 80 inches (203 centimeters) per year. Therefore, it is grown in tropical or tropical areas.
Sugarcane takes about seven months to grow in tropical areas and about 12 to 22 months in subtropical areas. At this time, sugarcane fields are tested for sucrose, and mature fields are picked first. In Florida, Hawaii, and Texas, standing cane is pulled to burn dry leaves. In Louisiana, sugar cane is cut 6 to 11 feet (1.8 to 3 meters) tall and placed on the ground before being burned.
In the United States, harvesting (of sugar cane and sugar beets) is mostly done by machine, although in some states it is done by hand. The sugar cane brought in by truck or train is transported to the food processing plant for processing into powdered sugar.
The latest technology used in different stages of sugar production
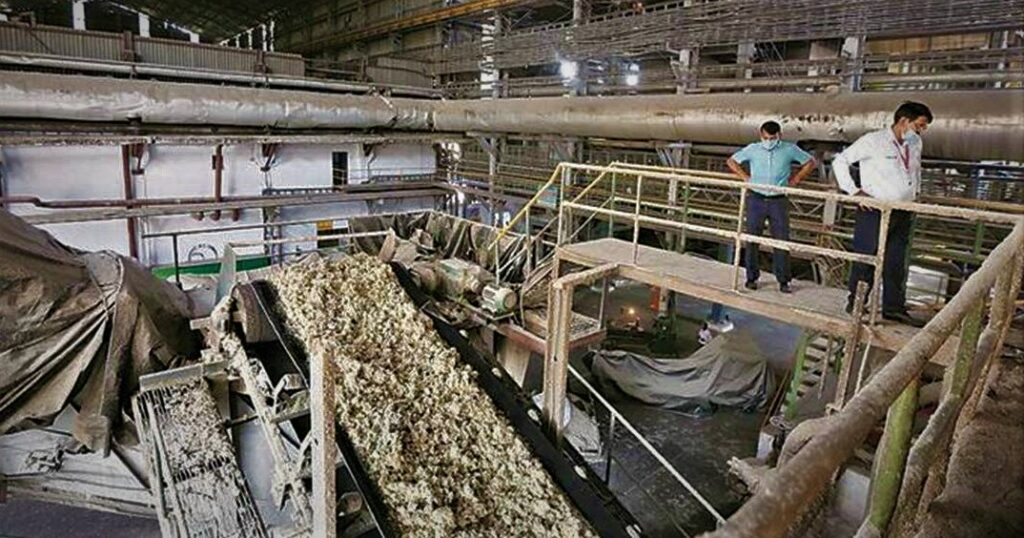
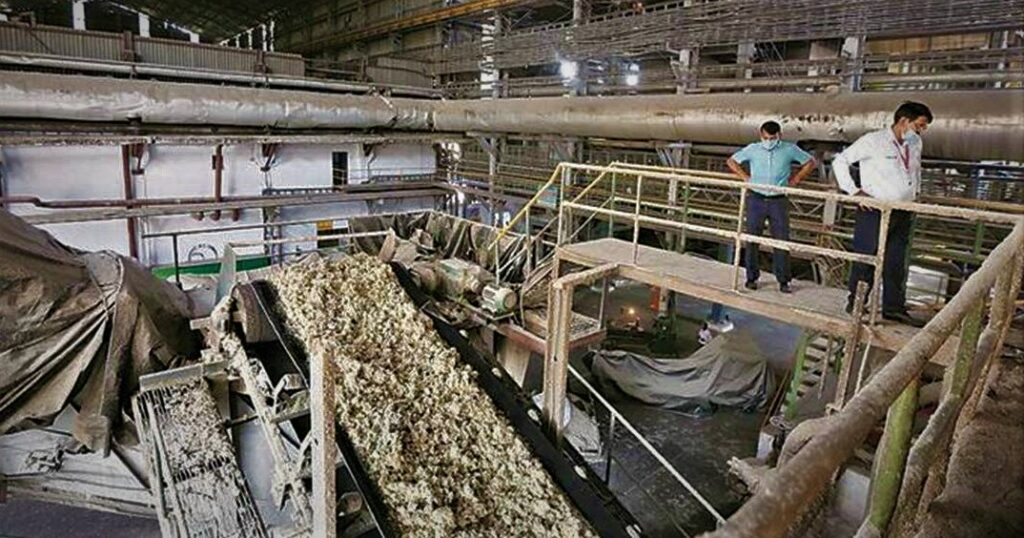
Baggase Drier Unit
Sugar mills generate electricity for internal consumption and surplus
electricity is sold in the national grid. Improve the use of fuel, i.. bagasse and boiler water
is an important production process for other income from the sugar industry. From
use a bag, the efficiency of the light can be greatly increased because
bagasse water reduction.
A few companies in India have developed a bag washing department for
reduce the moisture content of the bagasse as much as possible before feeding it
use hot water. This process uses flue gas as a heating medium for bag drying
i.e. the concept of heat recovery
MCU Moisture Control Unit
The water percentage of the bag plays a very important role in crushing and processing of wood.
A lot of work has been done in this area. Compared to the Bagasse Drier unit,
MCU is a structure developed with the aim of reducing the water content of
Bagasse to some extent.
The humidity control unit shows promising results and can be used
a tool for improving the value of the plant as a whole. The “Unit Control Unit” is designed to reduce the humidity of the outgoing bag
by leaving a pinch of each grinder, for another juice drainage
reducing the final moisture content of the bagasse. This ultimately improves overall performance
of the whole tandem in terms of total crusher extraction and final liquid % Bagasse
High Pressure Boilers
The fact that increasing the pressure of hot water increases the amount of steam and fuel is
what is established. This increase in the amount of steam and fuel is due to the higher feed
provides water heat by heating and reviving it (system
Efficiency is higher than cycle efficiency without regeneration) and higher
Boiler performance due to high pressure boiler design parameters. In general,
efficiency measures or high efficiency plant power if of
cogeneration pressure than that of low pressure, keeping the other channels of the system
group.
Automation
The sugar manufacturing process can be controlled and automated using a
Distributed Control System (DCS). Some automations are often used in
The sugar factories are:
speed control of bagasse bags,
Crusher speed control,
Project Management Engine,
turbine operation control,
plant juice management,
Short Retention Clarifiers
Top Features of Clarifiers are
The holding time for drinks and explanations is only 45-50 minutes. Sulphite juice should always be served at a temperature of 103 to 104oC.
Flash tank – the work of the flash tank is very important for muddling because it
needs a full fire of steam from its smoke.
The flocculant dose will be automatic in the juice flow.